Copper Casting
Copper Casting
Key Features of the Copper Casting Process:
1.Mold Preparation: The process begins with the preparation of molds, which can be made from various materials, including sand, metal, or ceramic. The choice of mold material depends on the desired finish, the complexity of the part, and the production volume.
2.Melting the Copper: Copper is melted in a furnace at high temperatures, typically around 1,984°F (1,085°C). The molten copper is carefully monitored to ensure it reaches the appropriate temperature for casting.
3.Pouring the Molten Copper: Once the copper is molten, it is poured into the pre-prepared molds. The pouring process must be controlled to avoid turbulence, which can lead to defects in the final product.
4.Cooling and Solidification: After the mold is filled, the molten copper is allowed to cool and solidify. The cooling time can vary depending on the thickness of the casting and the type of mold used.
5.Mold Removal and Finishing: Once the copper has cooled and solidified, the mold is removed, and the casting is inspected for quality. Any necessary finishing processes, such as machining, polishing, or surface treatment, are performed to achieve the desired specifications.
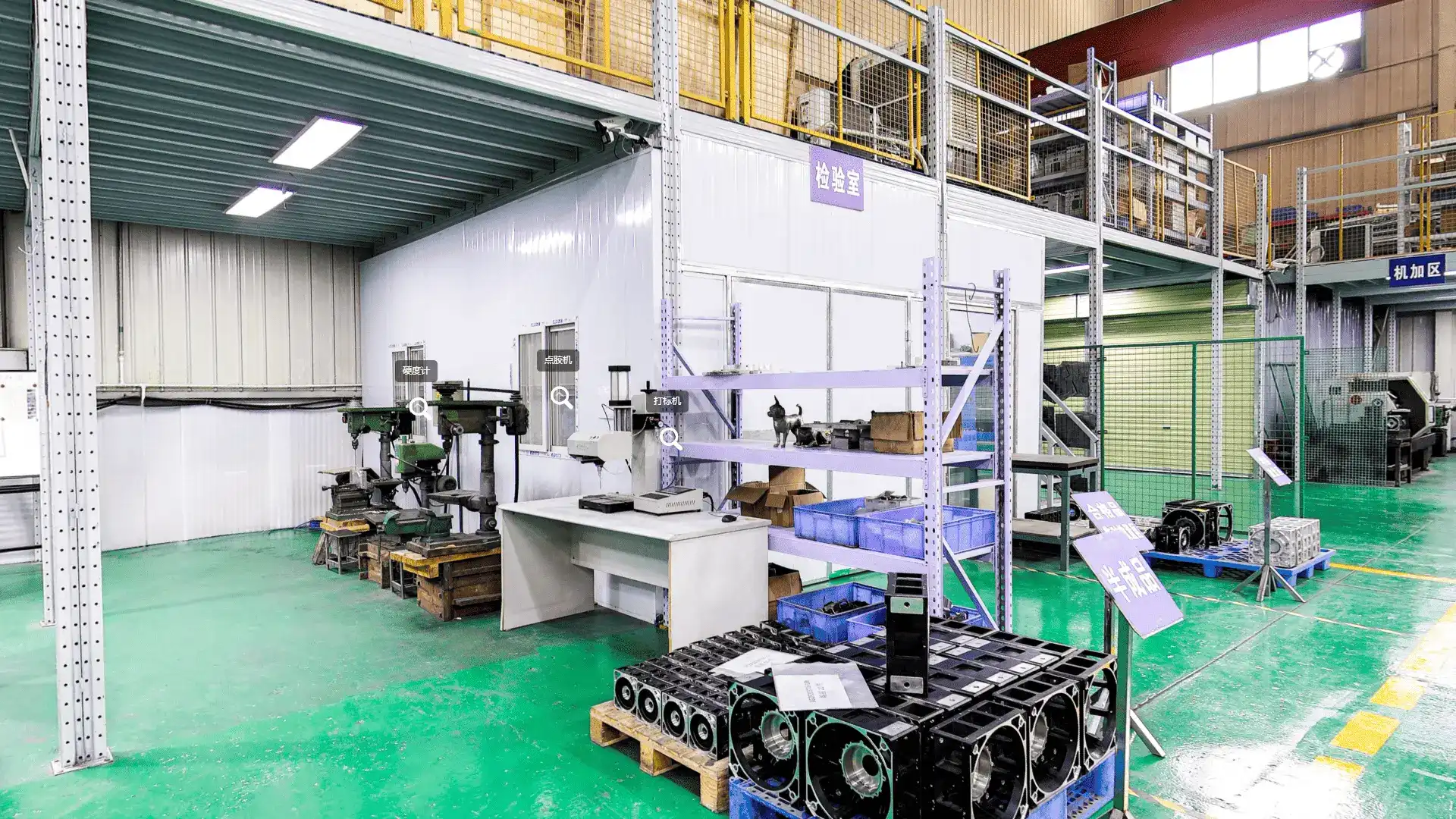
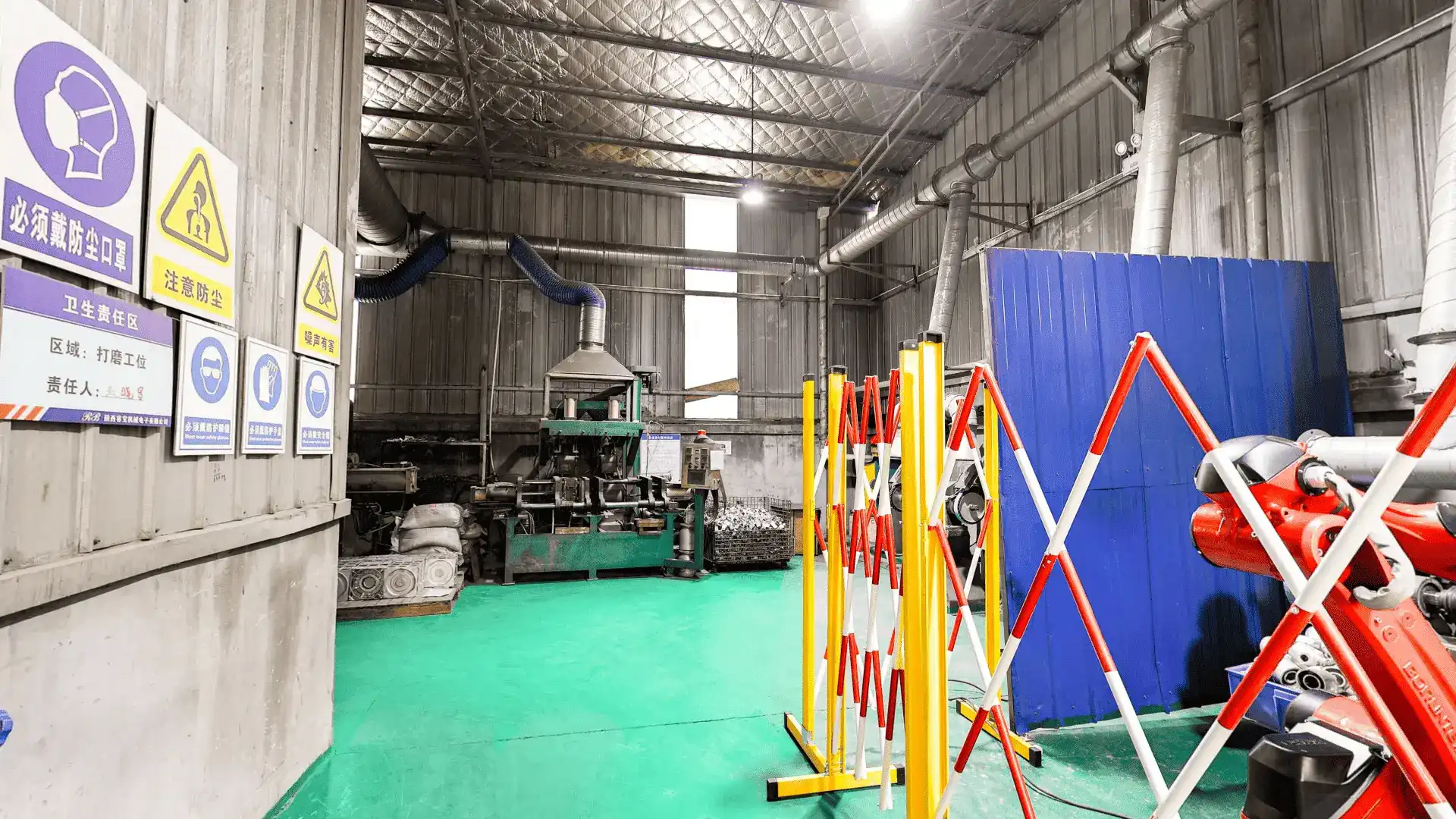
Advantages of Copper Casting:
① High Precision: Copper casting allows for the production of complex shapes with tight tolerances, making it ideal for applications that require high accuracy.
② Excellent Material Properties: Cast copper components exhibit superior electrical conductivity and thermal properties, making them suitable for a variety of applications.
③ Cost-Effectiveness: Copper casting is a cost-effective method for producing large quantities of components, especially when using reusable molds.
④ Versatility: The process can accommodate various designs and sizes, making it adaptable to different industry needs.
Copper casting is a reliable and efficient method for producing high-quality copper components that meet the stringent demands of modern engineering and design. By leveraging this process, manufacturers can achieve exceptional results while minimizing waste and maximizing efficiency.