Solutions
Our Solutions
Tailor-made, exclusive service, creating unique value for your needs.
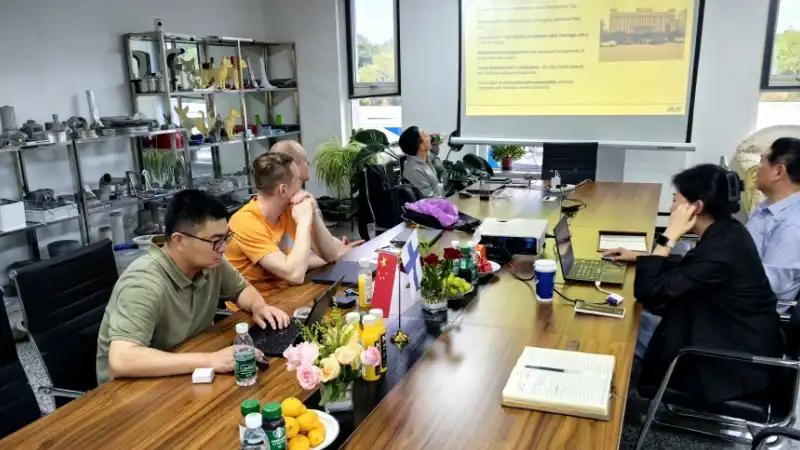
Customer consultation and demand confirmation
Demand communication: Customers make inquiries by phone, email or other channels, stating basic needs, estimated quantity, delivery date and other information.
Data preparation: Customers provide reference materials such as drawings, samples or molds to help us understand product specifications and technical requirements more accurately.
Preliminary evaluation: Based on the information provided by the customer, make a preliminary evaluation of the project feasibility, production cycle, cost, etc.
Quotation and contract signing
Plan formulation: According to customer needs and evaluation results, formulate a production plan, including material selection, process flow, quality standards, delivery date, etc.
Quotation: Provide customers with a detailed quotation sheet, including product unit price, mold fee (if any), packaging fee, transportation fee and payment method, etc.
Communication confirmation: The customer confirms the quotation, process, delivery date, etc., and the two parties further communicate on possible modifications or special requirements.
Contract signing: After confirmation by both parties, a formal contract (or order) is signed to clarify the delivery date, quality standards, payment terms and liability for breach of contract, etc.
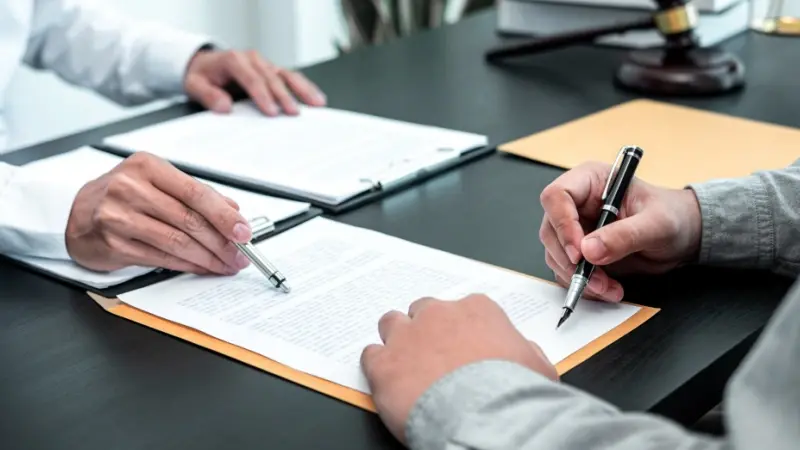
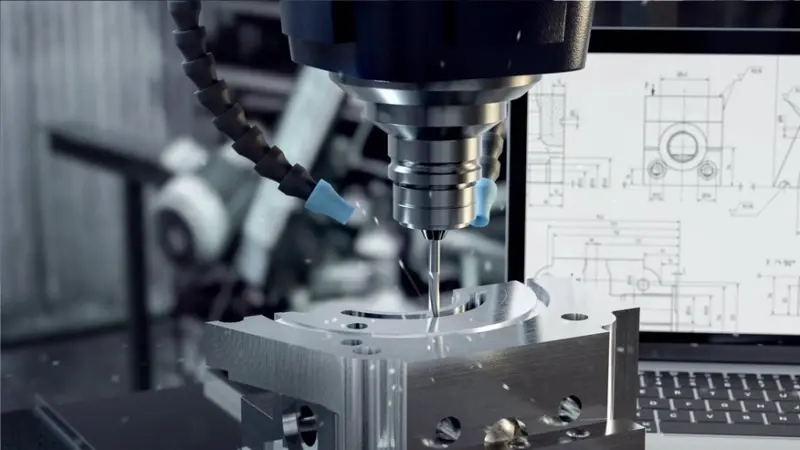
Production preparation and samples (if necessary)
Production data preparation: Prepare production process documents, technical parameter descriptions and other materials according to the confirmed drawings or samples.
Raw materials and molds:
If a new mold is required, arrange mold production or adjustment, and test it;
Prepare the required raw materials, auxiliary materials and tools.
Trial production/proofing: Proofing is carried out first as needed to confirm whether the sample quality, size and other requirements are met, and make adjustments if necessary.
Formal production and quality control
Formal production: After confirming that the sample is qualified, mass production is carried out, strictly following the process flow and quality standards.
Process inspection: Conduct quality inspections at key production nodes, make timely adjustments when problems are found, and ensure stable batch quality.
Completion inspection: After production is completed, the finished product is finally inspected in terms of appearance, size, performance, etc.
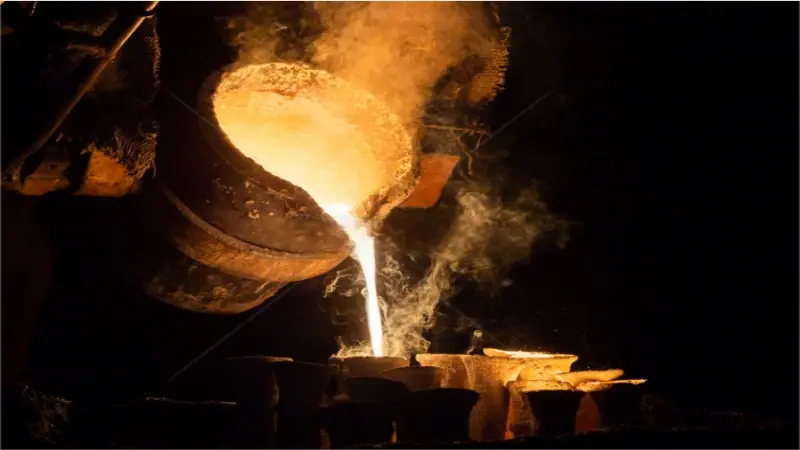
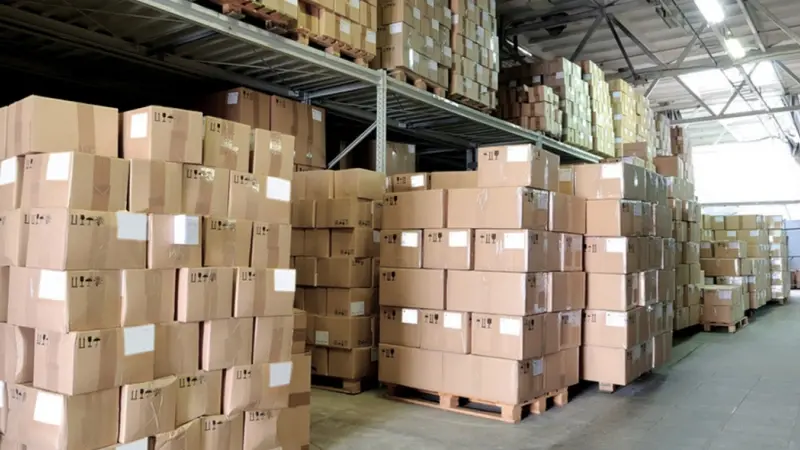
Packaging, payment and delivery
Packaging: Packaging is carried out according to the contract or customer requirements (such as conventional packaging, customized packaging, reinforced packaging, etc.), and relevant logos or labels are affixed.
Transportation preparation: Contact the logistics or express company (or the customer picks up the product by himself) to determine the freight, transportation method and delivery time.
Payment: According to the contract requirements, the customer makes payment (advance payment, final payment or other agreed payment methods).
Delivery: After receiving the payment, the goods will be delivered to the designated location according to the delivery time and method agreed in the contract and the logistics information will be promptly informed to the customer.
After-sales service
Arrival confirmation: Pay attention to the logistics progress, communicate with the customer in time after the goods arrive, and confirm the arrival of the product.
Feedback: Track product usage, understand quality and performance, and promptly answer customer questions or handle exceptions.
Continuous improvement: Analyze and improve the problems reported by customers, and optimize the process in future production or cooperation.
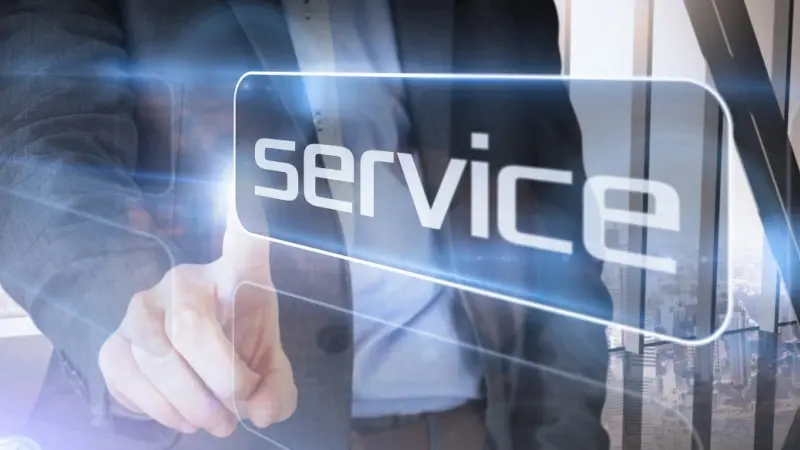