Low Pressure Casting
Low Pressure Casting
- VIEW MORELow Pressure Casting Robotic Arm Bracket
- VIEW MOREStator Housing
- VIEW MOREAluminum Door Handle
- VIEW MORELow Pressure Casting Gear Parts
- VIEW MORECast Impeller
- VIEW MORECasting Coupling Flange Parts
- VIEW MOREPrototype Aluminum Casting
- VIEW MORELow Pressure Casting Flange Parts
Key Features of the Low Pressure Casting Process:
1. Controlled Filling: The molten metal is drawn from a holding furnace and forced into the mold cavity through a riser tube. This controlled filling minimizes the risk of air entrapment and ensures a uniform flow, which is critical for achieving intricate designs and high dimensional accuracy.
2. Material Versatility: Low pressure casting is suitable for various metals, including aluminum and magn esium alloys, making it a versatile choice for different industry applications.
3. Enhanced Surface Finish: The process produces components with excellent surface quality, often reducing the need for additional finishing processes. This results in cost savings and shorter lead times for manufacturers.
4. Reduced Defects: The low-pressure environment minimizes common casting defects such as porosity, inclusions, and shrinkage, leading to stronger and more reliable components.
5. Applications: Low pressure casting is widely used in industries such as automotive, aerospace, and industrial equipment, where precision and durability are paramount.
By employing low pressure casting, manufacturers can achieve high-quality results that meet the stringent demands of modern engineering and design. This process enhances the final products' performance and contributes to more sustainable manufacturing practices by reducing waste and energy consumption.
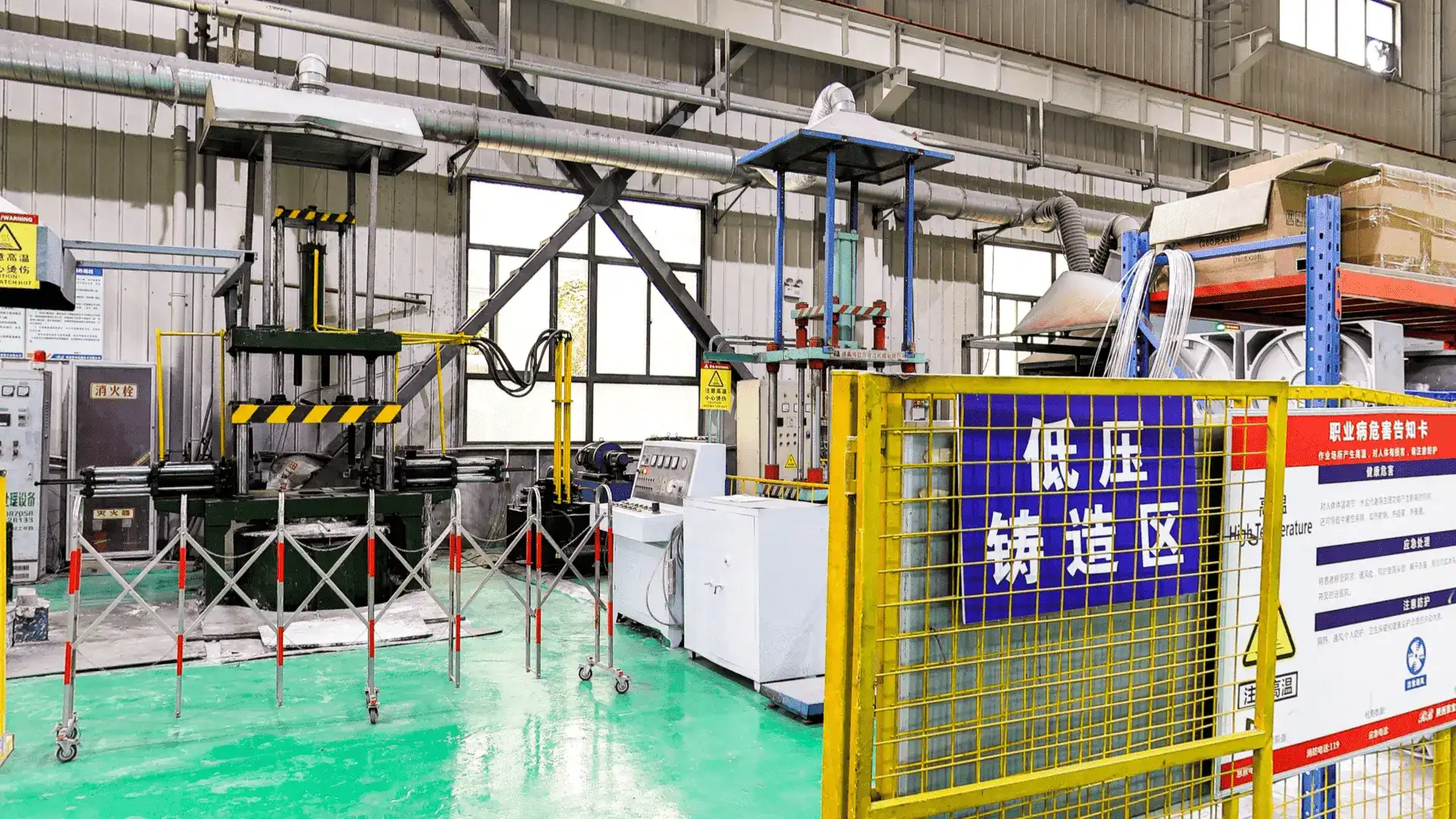
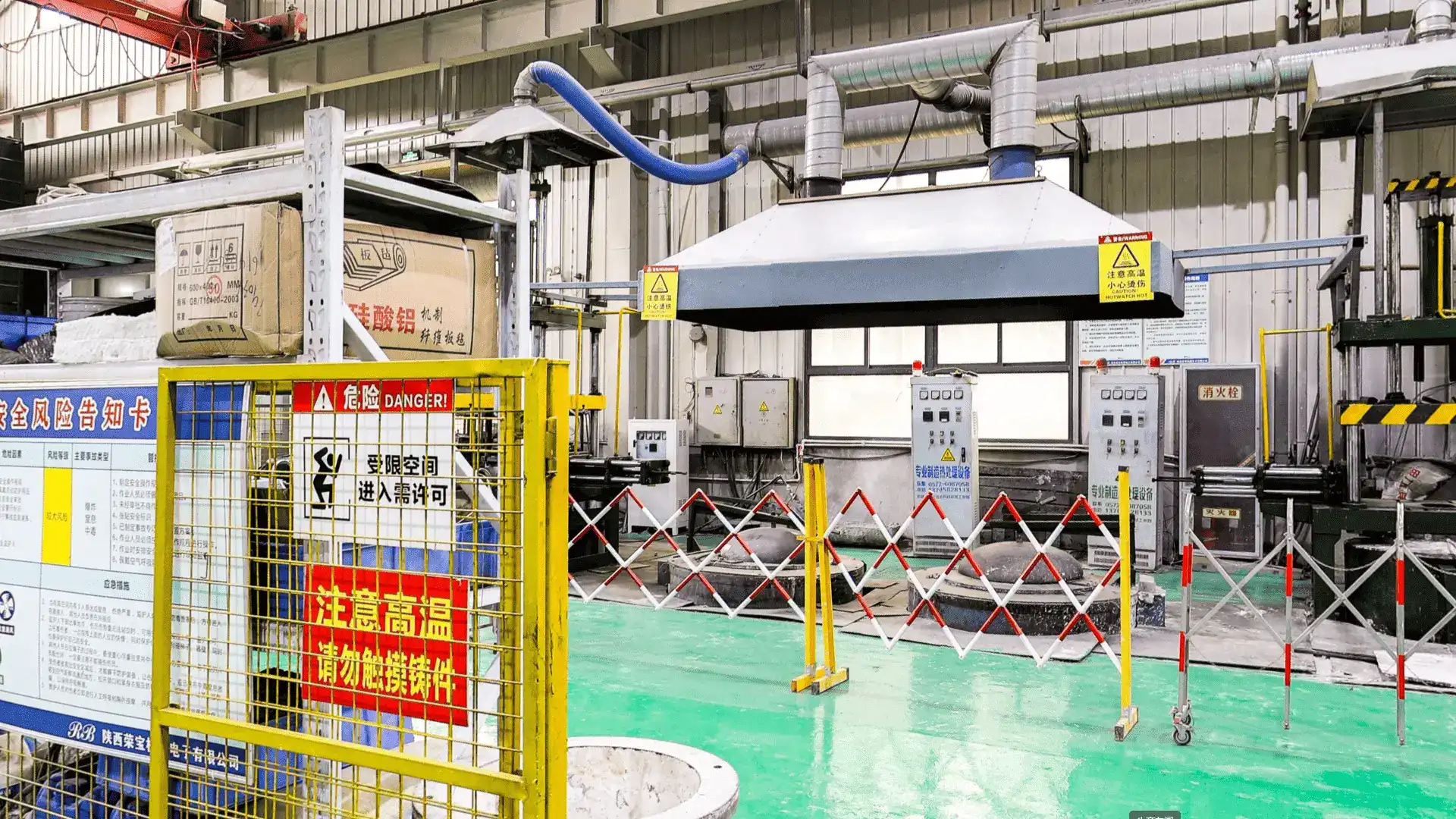